株式会社デジタルシアターが推進する製造業の「最初のデジタルトランスフォーメーション」は、製造プロセスの効率化だけでなく、企業文化やビジネスモデルそのものの変革を目指す取り組みです。40年以上にわたり蓄積した専門知識を活用し、単なる技術導入を超え、企業戦略の中核にデジタル技術を位置付けることで、顧客企業の成長と競争力を加速させています。特に、設計プロセスにおいて3Dモデリング技術を活用したロッキードマーチンのF35開発の事例に見られるように、デジタルツイン技術を駆使したリアルタイムでの状況把握や将来予測が実現し、従来のプロセスとは比較にならないほどの効率化と革新性をもたらしました。デジタルシアターが提供する精密なソリューションは、日本とEUの市場ニーズや技術基準の違いを熟知した上で構築されており、20年以上に及ぶCADデータの品質向上の実績に裏付けられています。これにより、顧客企業は新たなビジネス機会を最大限に活用できるのです。さらに、複雑な課題に対応する実用的サポートを通じ、変化への柔軟性を企業文化として浸透させることで、長期的な競争優位性を築いています。これこそが最初のデジタルトランスフォーメーションの真の価値です。
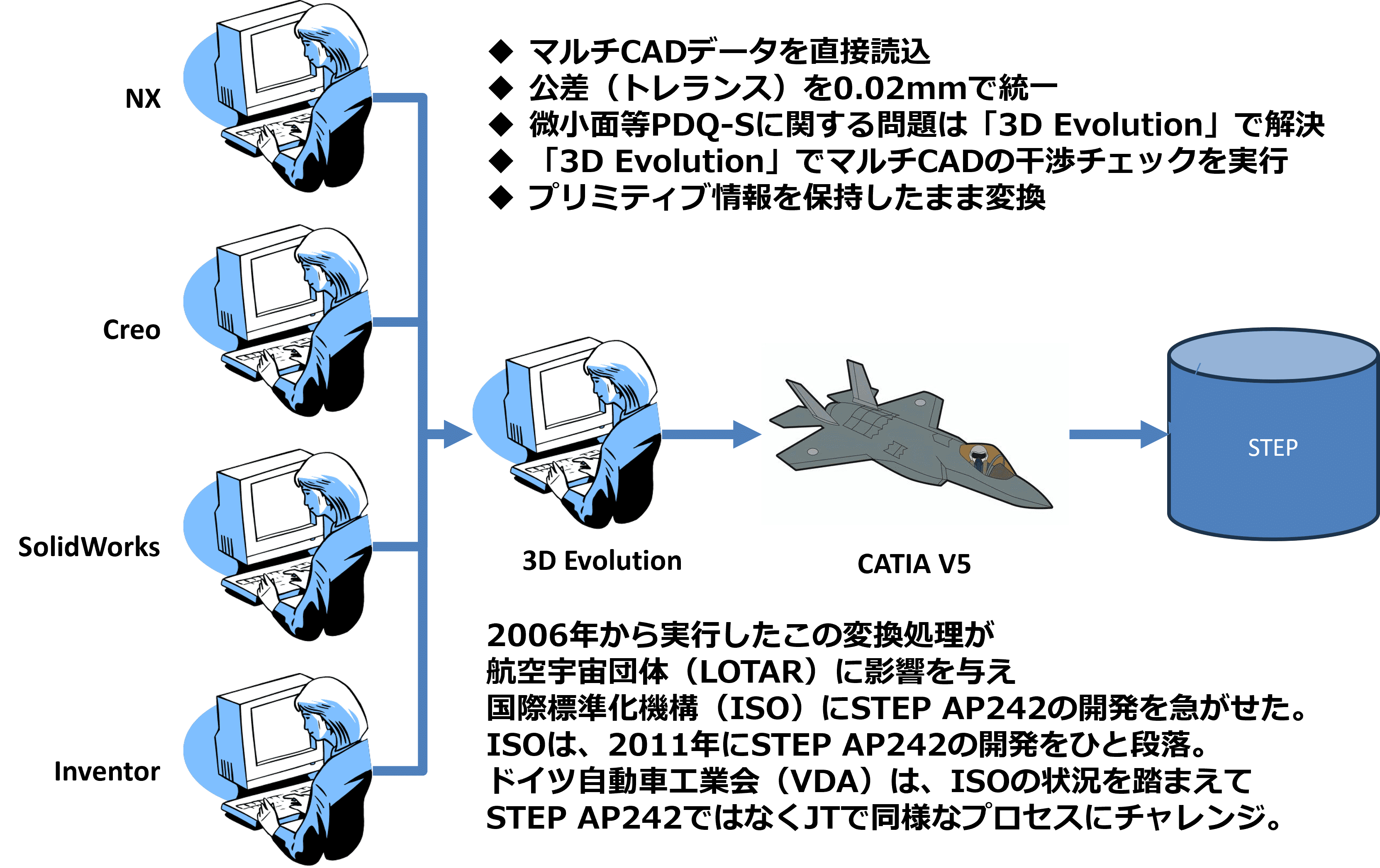
> F35の開発成功が3D図面の成功をもたらした
F-35戦闘機の開発成功は、3D図面を活用した設計プロセスの進化が大きな要因となっています。従来の2D図面に比べ、3D設計は部品間の適合性をリアルタイムで検証できるため、設計ミスの低減と製造精度の向上が実現しました。さらに、多様なCADシステムを統合したことで、国際的な開発チームが一元化されたデータを基に協力しやすくなり、開発効率の向上につながりました。また、3Dデータを活用したPDQ(Product Data Quality)の最適化により、設計段階でのデータ品質を高め、製造時のトラブルを最小限に抑えることが可能となりました。これらの要素が相まって、F-35の開発成功を支える堅固な基盤が形成され、航空機設計の新たな標準が確立されたのです。この技術的アプローチは航空機産業にとどまらず、他の製造業にも大きな影響を与え、今後の設計・製造プロセスのさらなる発展を促す可能性を秘めています。以上のように、3D図面の活用はF-35開発の成功を導いただけでなく、製造業全体の革新を加速する重要な技術基盤となったのです。