株式会社デジタルシアターは、日本の製造業が抱える課題として知られる3D図面技術の導入遅れに対して、多面的な解決策を提供しています。日本の製造業が3D図面への移行が進まない原因には、長年続いてきた2D図面主体の文化的な要因や、高度な3D技術を活用できる人材不足といった技術的な課題があります。デジタルシアターでは、40年以上にわたるCADデータ品質向上の経験を活かし、単なる技術支援を超えて企業文化やビジネスモデルを変革するソリューションを提供しています。地域特性に応じた精密なサポートを通じて、企業が新しい技術導入に伴う困難を乗り越え、長期的な競争優位性を築くことが可能になります。3D図面導入を阻害する課題を理解し、包括的なアプローチでその解決をサポートすることこそ、日本の製造業がグローバル市場で再び競争力を高めるために不可欠です。
> 日本には欧州と同等な3D図面のテスト環境がない
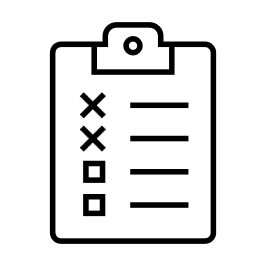
日本の製造業は、かつてその精密技術と革新力で世界をリードしてきましたが、現在、3D図面のテスト環境の不足という課題に直面しています。欧州では、ISOやLOTAR、VDAといった国際的な組織が主導し、3D Evolutionや3D Analyzerなどのツールを活用して、3Dデータの標準化と検証環境を整備しています。一方、日本では、こうした環境の構築が遅れており、3Dデータの長期的な運用や品質保証が十分に行われていません。これにより、製品設計の精度やデータの互換性が確保されず、国際市場での競争力が低下するリスクが生じています。また、3D図面の検証環境の未整備は、企業のイノベーションを阻害し、新たな設計手法の確立や製造プロセスの効率化の機会を失わせる要因にもなっています。しかし、この問題を解決するための技術やノウハウはすでに存在しており、産学官が連携し、標準的なテスト環境の確立を進めることで、日本の製造業は再び世界の最前線に立つことが可能となります。今こそ、3D図面のテスト環境の整備に取り組み、日本のものづくりの競争力を強化する時です。
> 3D図面が進まない理由
● テスト環境の整備不足により、3D図面の潜在能力が活用できていない。
● 異なるCADソフト間の互換性検証が不足し、国際競争力を損なっている。
● イノベーションの機会が制限され、新技術開発が進みにくい状況である。